Out of Thin Air
An inside look into FCA US LLC’s Aero-Acoustic Wind Tunnel
With only four full-scale, dedicated, automotive wind tunnels in the United States (and two more under construction), the Aero-Acoustic Wind Tunnel at FCA US LLC Headquarters in Auburn Hills, Michigan, and the scary smart aerodynamicists who use it are the go-to resources for testing FCA US vehicles, including race vehicles.
How It Began
Chrysler Corporation began talks on building the first reduced-scale wind tunnel in 1927. Words tuned into action and a 1/10 scale wind tunnel was built and testing began. This would be one of the first dedicated automotive wind tunnels in the world.
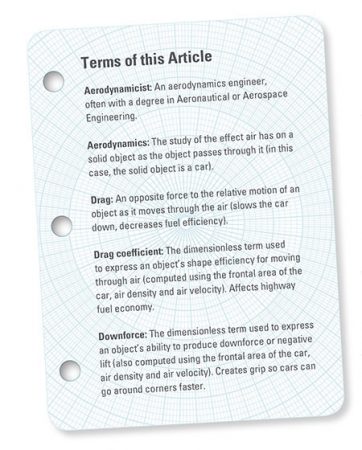
By 1930, testing had led to the application, and the 1934 Chrysler and De Soto Air Flow vehicles were born. Coupe and Sedan models were available. These cars were among the first production vehicles to utilize wind tunnels and aerodynamics prior to entering the marketplace.
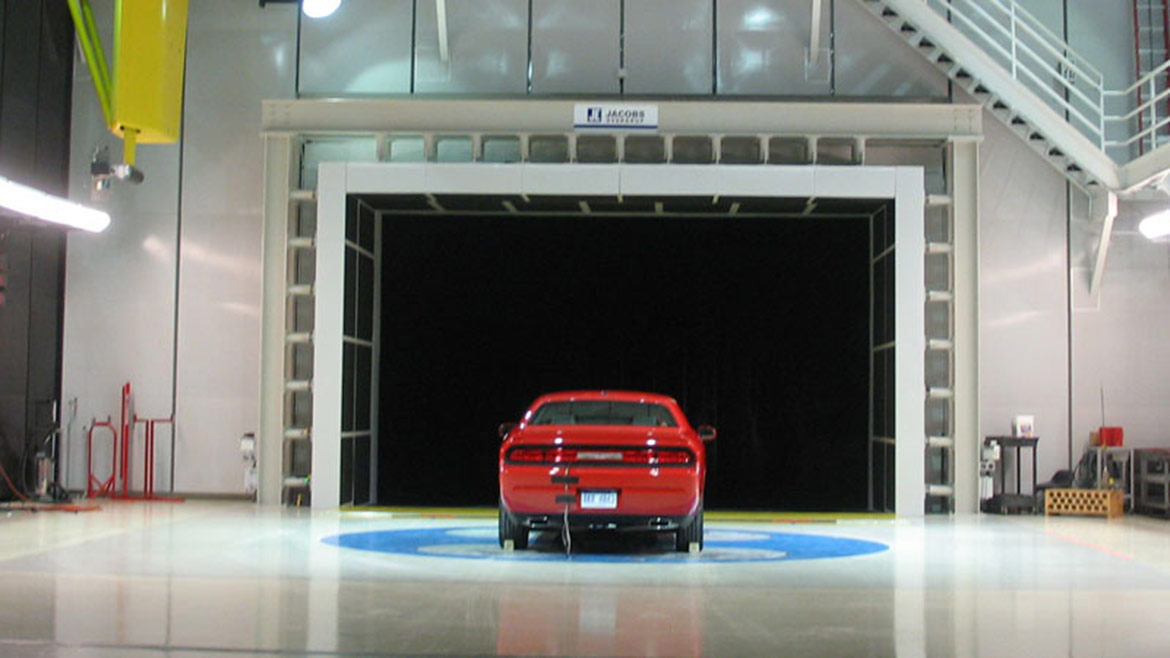
Ebbs, Flows and the Aero-Evolution
The Great Depression took its toll on the “Air Flow” models, and Chrysler Corporation stopped production in 1937. The fascination with aerodynamics resurfaced in the marketplace in the 1950s with styling effects like tail fins.
In the 1960s, when Chrysler Corp. was deep into stock car racing, the public really got a taste of aerodynamics and its effects on speed and handling. Chrysler Corp. took 30+ years of learning to the track with the Dodge Charger Daytona and Plymouth Superbird. Both vehicles experienced extensive wind tunnel development and track testing. The combination proved to be the perfect recipe for success with an 80% win rate in 1970.
By 1973, conflict with the Middle East resulted in a U.S. oil embargo, which made aerodynamics a key consideration for the FCA US vehicles. This time, they used their techniques to develop low-drag and fuel-efficient daily drivers.
Now in the 21st century, FCA US continues to be among the leaders in the industry in aerodynamics with the development of racing, performance and production vehicles.
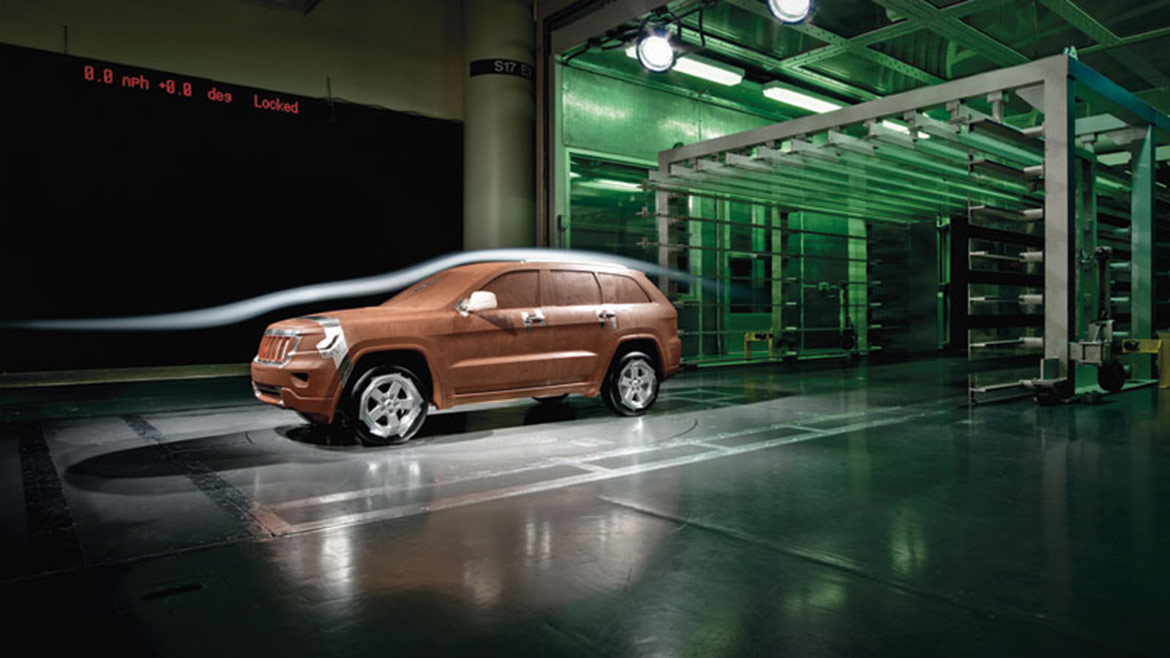
Production Vehicle Testing
When it comes to the wind tunnel testing of production vehicles, fuel efficiency is the primary goal. FCA US aerodynamicists report aerodynamic drag in terms of the drag area. This is the drag coefficient multiplied by the frontal area of the vehicle. The drag coefficient is the vehicle’s non-dimensional shape efficiency. The scale factor is the frontal area. The drag area relates directly to the horsepower required to overcome aerodynamic drag and is the primary consideration for improving highway fuel economy.
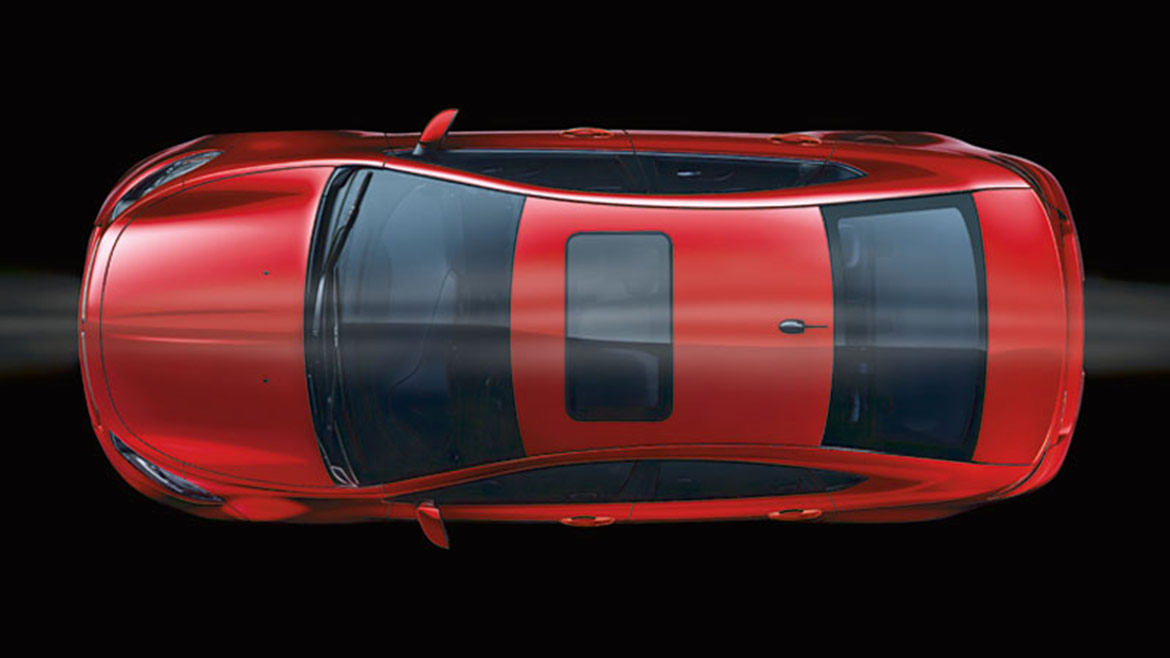
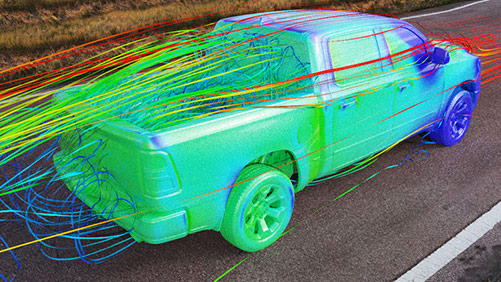
Aerodynamics testing and analysis begins several years before the start of production, “We work concurrently with our Product Design Office to ensure FCA US products are beautiful and efficient,” said Greg Fadler, Manager of Aerodynamics Engineering and Wind Tunnel Operations.
That begs the question: If the model isn’t in production, how can it be put into the wind tunnel for testing?
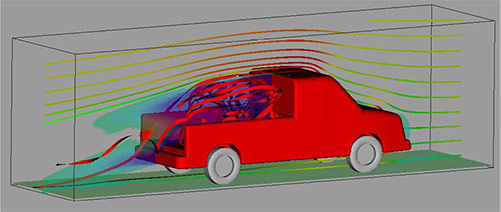
There are actually two wind tunnels at the FCA US facility. One is full-scale, and one is 3/8 scale for early testing. 3/8 scale clay models of all new vehicle designs are created and refined in the wind tunnel. These small clay models are extremely detailed – complete with 3D printed engines, transmissions, exhausts, belly pans and suspensions. They are as close to their real vehicle counterparts as possible.
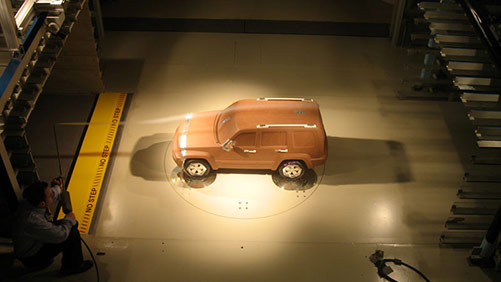
“We test and refine the small-scale model almost until we go to production,” said Fadler, “We also build full-scale models and optimize them later in the process. Finally, we test the early production models to validate all of our previous work. Two of our recent achievements are the 2019 Ram 1500 and the 2018 Jeep® Wrangler. We improved the aerodynamic drag of both new models by 9% over the vehicles they replaced. That’s huge in our world, considering that a typical program improvement of 3% to 5% is considered good.”
Performance Vehicle Testing
Optimization of aerodynamics is different for regular production, performance and racing vehicles.
Regular production vehicles strive for maximum fuel efficiency and are speed limited so high-speed performance development is simplified.
The main goal for race vehicles is maximum speed. Therefore, the focus is the optimum balance between downforce and drag to achieve the best possible elapsed times. Of course, predictable handling and high-speed stability are enablers to this goal. While still important in most forms of racing, drag coefficient and fuel economy are usually secondary considerations to maximum performance on a race vehicle. Aerodynamic efficiency is the lift-to-drag ratio (or downforce-to-drag ratio). Optimization of this term is specific to each race track. The range of L/D values are predetermined so the racecar can be set up for minimum lap times at each race track and the current weather conditions. In similar terms, increasing downforce improves the speeds through corners, which is critical in most forms of motorsports.
SRT® models strike a different balance between efficiency and performance than regular production and race vehicles. SRT products must still achieve the best possible fuel economy while delivering excellent handling and high-speed stability throughout their operational envelope.
For each vehicle type, regular production, SRT and race vehicles, wind tunnel testing allows the FCA US Aero Team to measure drag, lift, side forces, rolling, pitching and yawing moments. Optimization of these six aero parameters is specific to each vehicle type and application.
The FCA US full-scale wind tunnel utilizes two boundary layer control systems, a suction slot and tangential blowing slot. These two features work in harmony to minimize the boundary layer thickness under the vehicle. The boundary layer is the thin region between full-speed flow and non-moving flow at the floor. The thinner the boundary layer, the better the wind tunnel simulates the real world. The full-scale wind tunnel’s nozzle size is a large 300 square-feet, which is large for an open-jet, automotive wind tunnel. The tunnel can also test vehicles in +/-180 degrees of yaw, allowing it to produce winds on the vehicle from every possible angle, including backwards! The wind tunnel’s weigh-beam balance system is accurate to within +/-0.01%.
Ultimately, the goals of the FCA US Aero engineers, facilities and testing are obvious. They are all focused to deliver excellent results for production, performance and racing vehicles.
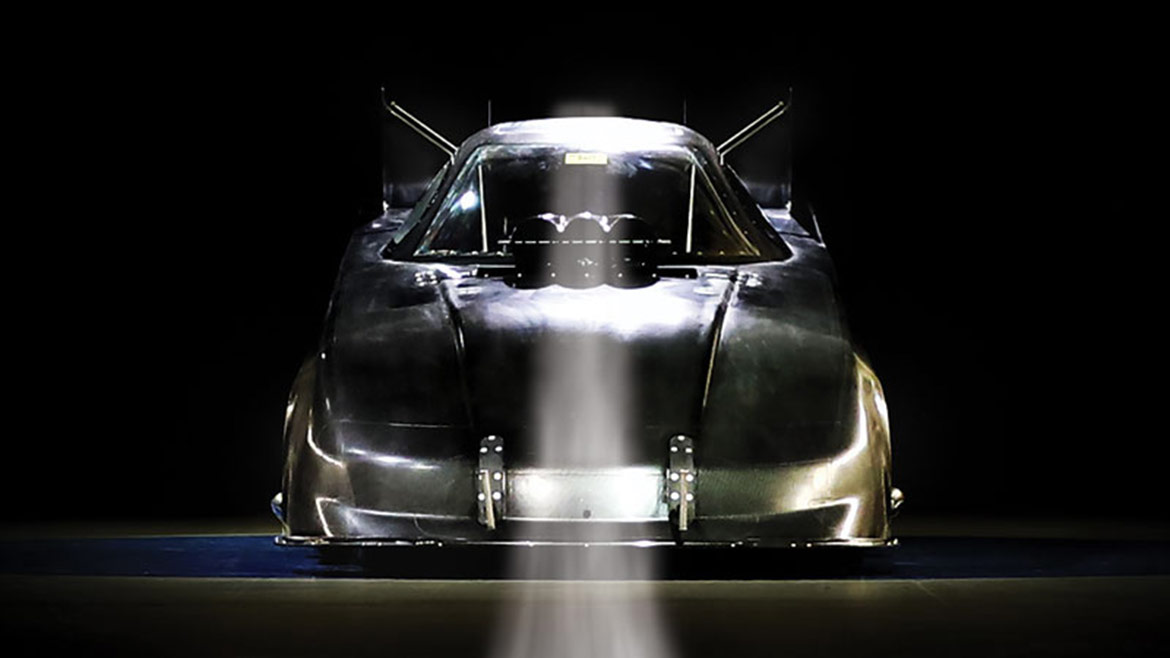
0 Comments